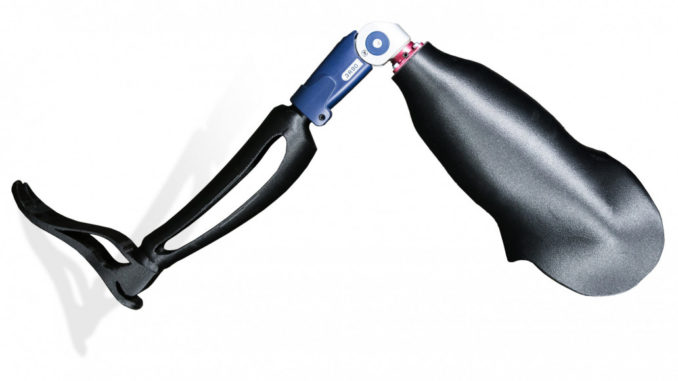
Compania de produse chimice BASF și furnizorii de soluții industriale 3D Essentium au încheiat un parteneriat pentru manufacturarea de suporturi pentru proteze din fibră de carbon termoplastică tipărite în 3D.
Astfel, clinicienii pot personaliza cu ușurință accesoriile protezelor pentru a oferi o potrivire mai confortabilă pentru pacienți.
Folosind poliamidă Ultramid de la BASF cu fibră scurtă de carbon, protezele tipărite cu tehnologia 3D sunt mai ușoare și mai dure. În același timp, ele sunt mai flexibile decât fibrele de carbon tradiționale.
Materialul din termoplastic facilitează ajustările mici de 2-3 mm, pentru a se adapta la schimbările fizice ale pacienților.
Suporturile au fost testate de clinicieni și pacienți la sediul Clinici din USA Anew Life Prosthetics and Orthotics (ALPO). Clinica ALPO a validat tehnologia și a furnizat un feedback real al pacientului. Potrivit lui Chris Casteel, proprietarul clinici ALPO:
„La fel ca orice alt produs, este un lucru sa auzi despre el și este un alt aspect să simți și să-l atingi în realitate. Am primit un răspuns extrem de pozitiv de la pacienți pentru suporturile de testare tipărite 3D. Este incredibil să vezi și să simți cât de bine se potrivesc. Este un succes imens pentru industria protezelor și aștept cu nerăbdare să văd ce urmează. ”
Imprimarea 3D accelerează în mod semnificativ dezvoltarea protezelor
Deși FDA nu reglementează în mod oficial protezele imprimante 3D, Essentium și BASF au ales să adere la standardele stricte stabilite de instituția FDA pentru reglementarea producției de aditivi (decembrie 2017). Ghidul oferă un plan de fabricare ce constă din 30 de etape, iar dispozitivele sunt inspectate manual înainte de a fi expediate.
În mod tradițional, clinicienii au nevoie de trei zile pentru turnarea suporților de fibră de carbon. Imprimarea 3D a redus în mod semnificativ acest proces la doar 24 de ore. În plus, dezvoltarea minimizează erorile de fixare, iar piesele rareori necesită ajustări. Blake Teipel, președinte și co-fondator al Essentium, a adăugat:
„Materialele utilizate în conceperea suporților definitivi oferă pacienților o mobilitate mai mare și mai multă libertate. Tiparirea 3D ne facilitează să realizăm o proteză personalizată, mai ușoară, mai accesibilă și mai confortabilă pentru pacient și permite ca procesul de producție sa fie mai ușor și mai eficient pentru clinician.”
În viitor, cele două companii speră să fabrice proteze tipărite 3D care includ elemente rigide și flexibile TPU. Acest lucru poate crește confortul și este de așteptat să fie lansate în acest an (2018).
Sursa: all3dp.com
Lasă un răspuns