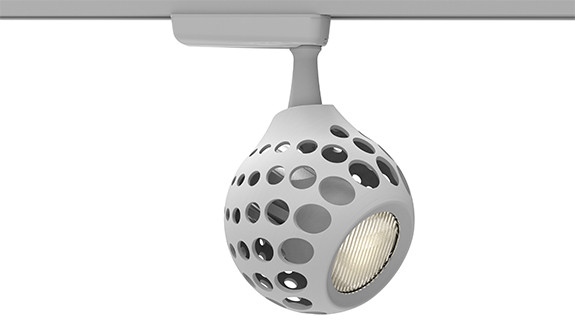
LimeLite este un producător de corpuri de iluminat cu sediul în Swinburne, Australia, iar pentru a crea noua gama de corpuri de iluminat eficiente a lucrat împreună cu designeri de produs de la Școala de Design Swinburne.
Aceasta nouă serie de corpuri de iluminat este specială pentru că, desenele sunt complexe și se pot realiza numai prin utilizarea tipăririi 3D. Noua serie de corpuri de iluminat a fost denumită „On track”.
Motivul asocierii dintre producătorul de corpuri de iluminat și școala de proiectare a fost acela, de a afla dacă este posibilă integrarea imprimării 3D în producția comercială. Producătorii au adaugă că, utilizarea acestei tehnologii în producția corpurilor de iluminat era o necunoscută.
Designerii împreună cu producătorii de produs, au lucrat la cercetarea pieței timp de 11 luni. Însă, au vrut să descopere modalități noi de a integra componente electronice în carcase imprimate în 3D.
„Fără echipa Swinburne, această serie pur și simplu nu ar fi fost posibilă. Suntem foarte incantați de gama On Track și de potențialul său de export „, a declarat Paul Hearne, CEO al LimeLite Sales și Marketing.
LimeLite OnTrack oferă cinci corpuri de iluminat imprimate 3D
Noile corpuri de iluminat vor fi disponibile începând cu luna octombrie. Fiecare corp de iluminat este imprimat cu tehnica 3D, iar procesul durează între 10 până la 30 de ore, pentru că au o forma delicată.
LimeLite utilizează un amestec de ABS și alte materiale. Acest amestec asigură rezistență la căldură și îndeplinește cerințele standardelor de proiectare a corpurilor de iluminat.
Anterior, LimeLite utiliza turnarea prin injecție pentru construcția de corpuri de iluminat din plastic. Dar, de când a decis să utilizeze tipărirea 3D, compania a investit bani în 30 de imprimante 3D Zortrax M200.
Imprimantele 3D de ultimă generație sunt găzduite în fabrica Thomastown din Melbourne. Cu toate acestea, un angajat lucrează exclusiv cu imprimantele, pentru a se asigura că producția merge pe drumul corect.
„Partea cea mai interesantă a acestui proiect, a fost crearea de modele cu adevărat unice fără constrângerile de fabricație ale pieselor turnate prin injecție din plastic. Imprimarea 3D permite crearea unor geometrii complexe, spre deosebire de turnarea clasică prin injecție.”
Utilizarea imprimantelor 3D evită investițiile masive în retehnologizarea și riscul scăzut al unui design scump, și nepopular care rămâne pe raft. Dacă nimeni nu comandă, pur și simplu nu se tipărește „, explică profesorul Blair Kuys, președintele departamentului de arhitectură și design industrial al companiei Swinburne.
Sursa: all3dp.com
Lasă un răspuns